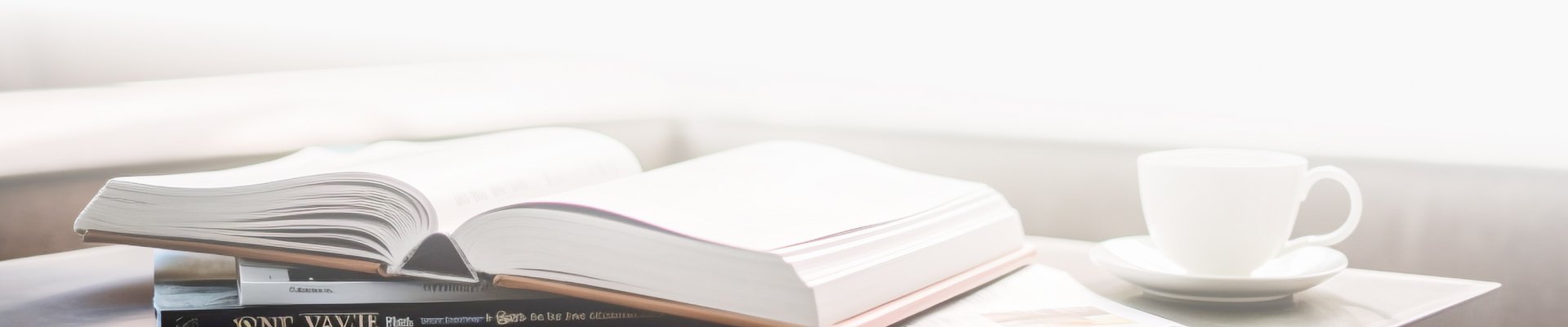
This article reveals the difficulties and trends of UVC LED packaging materials / processes / technologies
2021-08-31
As the traditional LED industry has entered a mature saturation stage, manufacturers have adjusted their development strategy to expand the automotive lighting, plant lighting, UV LED, IR LED and other niche markets, as well as small spacing, Mini/Micro LED and other new display areas. Among them, in the field of UV LED, although many manufacturers have long had layout, the market acceptance of UV LED products in the past was not high. Therefore, the UV LED industry has been in the initial stage of development, especially UVC led with relatively higher technical difficulty and price.
However, since the spread of New Coronavirus pneumonia epidemic around the world, consumers' awareness of sterilization and sterilization has increased rapidly. Epidemic prevention opportunities have led to a surge in demand for UVC LED products, pushing Global Multi forces into the development of UVC LED technology, and also giving birth to various products. However, are all these products in line with relevant requirements?
In fact, many factors need to be considered in the selection of reliable UVC LED products. For example, different doses and irradiation time are required for different viruses and bacteria to achieve disinfection and sterilization effect. From the perspective of product production, there are many considerations in all links from epitaxial chip to packaging and then to finished products.
Particularity of UVC LED packaging form, process and material selection
At present, UVC LED packaging has three forms: Organic packaging, semi inorganic packaging (also known as "near inorganic packaging") and all inorganic packaging.
Organic packaging uses organic materials such as silica gel, silicone resin or epoxy resin, mainly including lamp, SMD, ceramic molding and other products. The overall technology is relatively mature, but the UV resistance needs to be further improved.
Semi inorganic packaging (also known as "near inorganic packaging") uses silicone materials with inorganic materials such as glass. All inorganic packaging avoids the use of organic materials in the whole process, and realizes the combination of lens and substrate by means of laser welding, wave soldering and resistance welding, which completely reduces the light attenuation problem caused by organic materials and the failure problem caused by wet and thermal stress, and can accurately and effectively improve the stability and reliability of UVC LED devices.
At present, semi-inorganic packaging products are still the mainstream in the domestic market. They are mainly composed of ceramic support with cup and quartz glass. The placement of lens is realized by coating anti UV glue on the edge area of ceramic substrate with cup. Specifically, glue dispensing is carried out at the top or step of the cup, and then covered with quartz glass for curing and bonding.
In the selection of materials, UVC LED packaging is different from general led. Firstly, quartz glass is selected because quartz is inorganic and will not be affected by ultraviolet light, and the transmittance of quartz glass to UVC band is high. Secondly, in terms of heat dissipation substrate, due to the low photoelectric conversion efficiency of UVC led, most of it is converted into heat, so aluminum nitride heat dissipation substrate with high thermal conductivity is generally used. In addition, UVC has a bad effect on glue. Therefore, the requirements for UV resistance of glue bonding glass and support are also higher than those of general LED packaging.
It is also worth noting that some manufacturers use alumina heat dissipation substrate. Aluminum nitride and alumina substrates belong to ceramic substrates. The main difference between them is that the thermal conductivity of aluminum nitride is much higher than that of alumina. The thermal conductivity of aluminum nitride is generally about 140W / mk-170w / MK, while that of alumina is only about 30W / MK.
Alumina ceramics are generally white and have low thermal conductivity. They are usually used in low-power products. However, alumina ceramics are brittle and easier to break than aluminum nitride, so it is easy to collapse in the process of dicing and cutting. Aluminum nitride ceramics are generally gray black and have high thermal conductivity. They are usually used in high-power products. In addition, there are alumina ceramics doped with carbon powder on the market, which also presents gray black, but the thermal conductivity is lower.
Thermal management and air tightness affect the quality of UVC LED packaging products
The quality of UVC LED packaging products is affected by heat management and air tightness, which are also the technical difficulties in the packaging link. Among them, thermal management directly affects the service life of UVC LED packaging products, and air tightness determines its reliability to a great extent.
UVC LED is sensitive to heat, and its external quantum efficiency (EQE) is low. Only a small part of electric energy is converted into light, while most of electric energy is converted into heat, which directly affects the service life of the chip. In view of this, at this stage, many products are mainly based on flip chip with high thermal conductivity aluminum nitride substrate. Aluminum nitride has excellent thermal conductivity, can resist the aging of ultraviolet light source itself, and can meet the needs of high heat management of UVC led.
In addition to materials, packaging process is also an influencing factor of thermal management. The packaging process is mainly reflected in the solid crystal technology, including silver paste welding, solder paste welding and Gold Tin eutectic welding.
Although silver paste welding has good adhesion, it is easy to cause silver migration and device failure. As for solder paste welding, since the melting point of solder paste is only about 220 degrees, after the device is pasted, it will melt again after passing through the furnace again, and the chip is easy to fall off and fail, affecting the reliability of UVC led.
Gold Tin eutectic welding mainly uses flux for eutectic welding, which can effectively improve the bonding strength and thermal conductivity between chip and substrate. In contrast, it has higher reliability and is conducive to the quality control of UVC led. Therefore, Gold Tin eutectic welding is mostly used in the market.
In the welding process, the problem of welding void rate is mainly involved. Welding cavity refers to the defect formed during the welding process between LED chip and substrate. It is in the state of cavity in appearance. It is an important index affecting heat dissipation. The lower the welding cavity rate, the better the heat dissipation effect, the longer the product life and the better the quality.
In terms of reliability, packaging form is one of the influencing factors, but the key is air tightness. In the semi inorganic packaging form, the glass lens and the ceramic substrate with cup are connected by glue to form a closed cavity. Since the closed cavity cannot be vacuumized, when the glue is thermally solidified, the air in the cavity is easy to be heated, expand and overflow, forming bubbles, and forming an air channel in serious cases. At this time, external water vapor and impurities can enter the interior of the product through bubbles and gas channels, causing pollution to materials such as chips and substrates, seriously affecting the air tightness of the product, thus affecting the light output and reliability.
It can be seen that air tightness has a great impact on the packaging quality of UVC led, and the process treatment technology is very key.
UVC packaging pattern: mainly semi inorganic packaging, supplemented by all inorganic packaging
Since this year, UVC LED has achieved certain breakthroughs in different technical fields, transmitting the signal that the industry is booming. Although, due to the problems of high cost and low light efficiency, UVC LED products can not completely replace medical sterilization UV mercury lamps. However, with the progress of technology, it is believed that UVC LED will slowly enter this market soon. Moreover, due to its small size and simple design, UVC LED has certain advantages over mercury lamp in the field of mobile killing and small space sterilization. From the current market application, UVC LED has been applied to surface sterilization (portable sterilization products, sterilization lamps, mother and baby products), water sterilization and air purification( Wen: Zhihu (LED analyst Wong, ledinside)
Qingdao fluorescent Innovation Technology Co., Ltd. has a professional postdoctoral team, focusing on the research of ultraviolet sterilization application. After years of deep cultivation in the ultraviolet industry, the company has obtained a number of national invention and utility model patents. At present, a number of sterilization module products have been put into the market. For more details, you can browse the company website www.qdyingguang.com, contact the company for WeChat's official account.